Extrusion Line for Spc Floor Covering Board Production
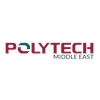
SPC Floor Covering Sheet Production Extrusion Line
SPC Floor Covering Extrusion Line is an advanced production system that produces Stone Plastic Composite (SPC) floor coverings by combining limestone and polyvinyl chloride (PVC). This line uses precise extrusion processes to produce durable and waterproof plates and tiles, providing superior durability and performance in various applications.
Features and Applications:
Main features include high cost performance and strong stability, while the high level of automation reduces labor requirements. The production process, simpler than LVT and WPC floor coverings, improves efficiency. Additionally, these lines offer comprehensive support with one touch, including workshop layout, equipment processing, installation, adjustment, personnel training, and complete solutions, enabling precise control of thickness and surface quality.
Various application areas of SPC Floor Covering Extrusion Lines include:
- Residential Floor Covering: Ideal for living rooms, bedrooms, and kitchens due to its durability and waterproof properties.
- Commercial Areas: Used for long-lasting floor covering solutions in offices, retail stores, and hotels with heavy foot traffic.
- Health Facilities: Suitable for hospitals and clinics where hygiene and easy maintenance are important.
- Educational Institutions: Preferred in schools and universities for classrooms and common areas.
- Industrial Areas: Used as durable floor coverings that can withstand heavy loads in warehouses and factories.
- Wall Covering: Can be used in decorative wall applications to add warmth and style to indoor spaces.
These applications showcase the durability, versatility, and aesthetic appeal of SPC floor coverings in various environments.
SPC Floor Covering Production Flow:
- Mixing:
Raw materials are weighed and mixed at 125°C automatically, then cooled to 55°C to ensure equal distribution and moisture removal.
- Extrusion:
The mixture is extruded using a twin-screw extruder, passed through four-roller calendars for thickness adjustment, and cooled before cutting.
- UV Coating:
UV coating is applied to increase durability.
- Cutting and Packaging:
The floor covering material is sliced, grooved, inspected, and packaged for distribution.
Technical Specifications of SPC Floor Covering Sheet Production Extrusion Line:
No |
Linery list |
QTY |
Description |
1 |
92/188 Conical Twin Screw Extruder |
1 |
800 kg/Hr |
2 |
Extrusion Mold |
1 |
|
3 |
4-Roller Calender |
1 |
|
4 |
Water Cylinder Thermostat Control Device |
1 |
|
5 |
Dual Working Position Pay-Off System |
1 |
|
6 |
Cooling Table |
1 |
12 Meters |
7 |
Edge Cutting Unit |
4 |
|
8 |
Puller Unit |
1 |
|
9 |
Cutter |
1 |
|
10 |
Stacker |
1 |
|
Assistant Line Equipment List |
|
||
1 |
Feeding Line |
2 |
|
2 |
Hot-Cold Mixer |
1 |
800/2000 |
3 |
Crusher |
1 |
37kw |
4 |
Milling Line |
1 |
90kw |
5 |
Cutting and Grooving Line |
1 |
Automatic or Semi-Automatic |
Extrusion Line for SPC Floor Covering
SPC extrusion line creates durable and rigid floor coverings by extruding the mixture of stone powder, PVC, and additives into sheets or plates. The process includes material preparation, extrusion, cooling, optional lamination, and cutting stages. SPC floor covering is known for its durability, stability, moisture resistance, and easy installation, making it ideal for areas with heavy foot traffic.
H3 Subheadings with Descriptions
Benefits of SPC Floor Covering Production Lines
SPC floor covering production lines offer many advantages:
- High Durability: Produces strong, abrasion-resistant, and scratch-resistant floor coverings.
- Moisture Resistance: Ideal for wet areas due to its waterproof feature.
- Efficiency: Provides fast production speeds and low material waste.
- Customization: Allows offering various sizes, designs, and surface finishes (e.g., embossed or matte).
- Environmentally Friendly: Reduces environmental impact by using recyclable materials.
- Cost Effectiveness: Reduces labor and maintenance costs with automated processes.
Customizing Your SPC Extrusion Line
Customizing your SPC extrusion line involves adjusting the following key factors:
- Material Formulation: Optimize the ratios of stone powder, PVC, and additives.
- Extruder Settings: Adjust speed, temperature, and pressure according to product requirements.
- Mold Design: Use molds suitable for the size and shape of the product.
- Cooling Systems: Optimize systems for homogeneous cooling.
You can adjust production speed, layer thickness, and surface finishes (e.g., embossed or matte) according to product requirements. Additionally, integrating automatic control and quality monitoring systems enhances consistency and efficiency. Customization enables the production of high-quality SPC floor coverings that meet market demands.
Maintenance and Troubleshooting Tips
- Regular Cleaning: Clean the extruder and mold regularly.
- Monitoring Temperature and Pressure Settings: Continuously monitor these settings for a balanced production process.
- Lubrication of Moving Parts: Regularly lubricate to ensure smooth operation.
- Cooling System Control: Conduct regular inspections to ensure system performance consistency.
- Calibration: Regularly calibrate the line to ensure thickness consistency.
- Use of High-Quality Materials: Prefer high-quality raw materials for long-term production.
- Wear and Tear Checks: Ensure long-term and uninterrupted operation by conducting routine checks on equipment.