108 Mm Upvc High Performance Pvc Window Profile Extrusion Line
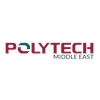
108 mm (110kg/h) High Performance PVC Window Profile Extrusion Line
PVC window profile extrusion line is a production system that shapes PVC material into window frames and related components by melting PVC. This process involves passing PVC through an extruder, shaping it into profiles through a mold, cooling and calibrating the shape, and cutting it to the desired size. This method typically produces durable, energy-efficient, and low-maintenance window profiles used in construction.
Features and Applications:
PVC window profile extrusion line features an extruder, calibration system, cooling unit, and cutting mechanisms to produce precise window profiles. It offers high customization for various shapes and sizes, provides strong control over material quality, temperature, and dimensions. Its applications include producing energy-efficient, low-maintenance window and door frames for residential, commercial, and industrial buildings. The line is also used for manufacturing other profiles like ventilation systems, trims, and reinforcement components.
Technical Parameters of 108mm High Performance PVC Window Profile Extrusion Line:
Technical Specs: |
Classic Type |
High-Speed Type |
|||||||
Type |
YF108 |
YF240 |
YF240A |
YF300 |
YF400 |
YF240 |
YF240 |
YF240A |
|
Maximum Width of Product (mm) |
108 |
240 |
150*2 |
300 |
400 |
240 |
240 |
150*2 |
|
Extruder Model |
SJZ55/110 |
SJZ65/132 |
SJZ65/132 |
SJZ65/132 |
SJZ80/156 |
SJP75/28 |
SJP93/30 |
SJP110/28 |
|
Maximum Extrusion Capacity (kg/h) |
110 |
180 |
180 |
180 |
320 |
150-250 |
250-400 |
400-500 |
|
Extruder Power (kw) |
22 |
37 |
37 |
37 |
55 |
45 |
55 |
90 |
|
Cooling Water (m3/h) |
7 |
8 |
8 |
8 |
10 |
7 |
8 |
10 |
|
Compressed Air (m3/min) |
0.6 |
0.6 |
0.8 |
0.6 |
0.6 |
0.6 |
0.6 |
0.8 |
PVC Profile Production Equipment Benefits
Usage of PVC profile production equipment provides high efficiency, precise molding, and customization possibilities for various profiles. These machines offer fast production with minimum material wastage, produce durable and low-maintenance products. Moreover, they provide a cost-effective solution by reducing labor and material costs. The use of recyclable materials supports eco-friendly production.
-
Choosing the Right PVC Window Frame Extrusion Line
-
When selecting a PVC window frame extrusion line, consider the production volume, design flexibility, and automation features for efficiency and productivity. By choosing a line from a reputable brand that offers low maintenance, energy efficiency, and reliability, you can ensure consistent quality and long-term durability.
uPVC Window Profile Extrusion Line
uPVC window profile extrusion line creates window frame profiles by melting uPVC material. This system produces durable, low-maintenance profiles for precise, efficient, and energy-saving windows.
Plastic Profile Extrusion Line Components
A plastic profile extrusion line typically consists of the following components:
-
Extruder: Melts and mixes raw materials.
-
Die: Shapes melted plastic into the desired profile.
-
Cooling System: Cools and solidifies the extruded profile.
-
Puller: Pulls the profile at a consistent speed and shape over the line.
-
Cutter: Cuts the profile to the desired length.
-
Control System: Monitors and adjusts temperature, speed, and other parameters for optimal performance.
These components work together to efficiently produce high-quality plastic profiles.
Advancements in PVC Profile Extrusion Technology
Recent advancements in PVC profile extrusion technology include:
-
Smart Controls: Enhanced PLC and IoT integration for real-time monitoring and automatic adjustments.
-
Energy Saving Features: Advanced motors and efficient heating systems that reduce energy consumption.
-
Fast Production: Improved screw and die designs for higher output and faster cooling.
-
Customization: More flexible systems that offer precise profile shapes, sizes, and multilayer designs.
-
Reduced Waste: Innovations in material processing and extrusion that reduce scrap rates and improve material usage.
These innovations enhance productivity, reduce costs, and support environmentally friendly production practices.