DS 1250 Rotierende Korbwaschmaschinen mit Stoßdämpfer manuelle Öffnung / Video
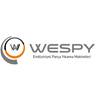
Rotary Basket Washing Machines With Shock Absorber Manuel Opening
The Wespy DS-1250 Rotary Basket Washing Machine is a powerful, high-pressure cleaning solution designed to effectively remove contaminants such as oil, sawdust, dirt, and other industrial residues from parts of various sizes and materials. Featuring a stainless steel rotative basket and a shock absorber manual opening system, this machine is built for heavy-duty use while minimizing water, detergent, and energy consumption. The DS-1250 is ideal for industries that require thorough cleaning with precision and efficiency, offering both reliability and cost savings.
Stainless Steel Rotative Basket: Parts are securely placed in a durable stainless steel rotating basket, which spins during the cleaning cycle to ensure that all surfaces are thoroughly exposed to the high-pressure water and degreaser mixture. The rotation provides consistent and uniform cleaning from multiple angles.
Shock Absorber Manual Opening: The DS-1250 features a shock absorber system that helps ease the manual opening and closing of the washing chamber. This system ensures smooth and controlled operation when loading and unloading parts, minimizing the risk of damage and improving safety.
High-Pressure Water Cleaning: The machine utilizes high-pressure water mixed with degreaser to effectively clean contaminants like oils, grease, sawdust, dirt, and residues from part surfaces. The pressurized water ensures that even the most stubborn dirt is removed efficiently.
Adjustable Time-Configured Water Nozzles: The DS-1250 comes with time-adjusted, pressurized water nozzles that can be configured based on the part structure and pollution level. The nozzles are designed to direct water at specific angles, providing optimal cleaning for various part shapes and contamination types.
Recirculation and Filtration System: The recirculation system filters the water during each cycle, allowing it to be reused multiple times. This reduces the need for fresh water and detergent, lowering operating costs while ensuring that the water used for cleaning remains clean and effective.
User-Friendly Operation: The DS-1250 is equipped with an easy-to-use control panel that allows operators to adjust cleaning parameters such as wash time, pressure, and nozzle settings. This ensures that each part is cleaned to the appropriate standards based on its size, shape, and contamination level.
Robust and Durable Construction: The machine is built with high-quality materials, including corrosion-resistant stainless steel, which ensures long-lasting durability even in demanding industrial environments. The robust design reduces maintenance needs and extends the lifespan of the machine.
Efficient and Compact Design: The DS-1250 is designed to optimize cleaning performance while maintaining a compact footprint. It fits easily into production lines without taking up excessive space, making it an efficient solution for various industrial applications.
Improved Cleaning Performance: The rotating basket and high-pressure washing system ensure thorough cleaning of parts from all angles. The adjustable nozzles provide customized cleaning based on the specific needs of each part.
Cost Efficiency: The recirculation and filtration system reduces water, detergent, and energy consumption, leading to lower operating costs. By reusing water and detergent, the DS-1250 makes the cleaning process more eco-friendly and cost-effective.
Time Savings: The efficient high-pressure cleaning system ensures quick removal of contaminants, significantly reducing washing time. The shock absorber manual opening feature also speeds up the loading and unloading process, improving overall production efficiency.
Enhanced Durability and Safety: The shock absorber manual opening ensures smooth, safe, and easy access to the washing chamber without risk of damage, reducing the likelihood of accidents during operation.
Versatility in Application: The DS-1250 is designed to clean a wide range of parts, from small components to larger industrial pieces. Its adjustable settings and versatile design make it suitable for various industries, including automotive, manufacturing, aerospace, and more.
Environmentally Friendly: By filtering and recirculating water, the DS-1250 minimizes water waste, making it an environmentally responsible choice for industries looking to reduce their ecological footprint.
Automotive Industry: Ideal for cleaning automotive parts, such as engine components, transmission parts, and metal brackets, that require removal of oils, grease, dirt, and contaminants.
Industrial Manufacturing: Suitable for cleaning metalworking tools, machinery parts, and industrial equipment exposed to oils, cutting fluids, dirt, and residues.
Aerospace Industry: Perfect for cleaning delicate aerospace components that need to be free from contaminants to ensure safe and reliable operation.
Electronics Manufacturing: Used for cleaning electronic components and assemblies that require a high standard of cleanliness for functionality and performance.
Heavy Equipment Maintenance: Ideal for cleaning components used in construction and mining machinery, which are often exposed to heavy dirt, grease, and grime.
General Industrial Cleaning: The DS-1250 is versatile enough to clean a wide range of parts across various industries, ensuring efficiency and optimal cleanliness in all applications.
The Wespy DS-1250 Rotary Basket Washing Machine with Shock Absorber Manual Opening provides a robust, cost-effective, and efficient solution for high-pressure parts cleaning. Its stainless steel rotative basket, customizable nozzles, and water recirculation system ensure that parts are cleaned thoroughly while minimizing resource consumption. The shock absorber manual opening system enhances safety and ease of use, making it ideal for demanding industrial environments. With its versatile applications and eco-friendly design, the DS-1250 is a reliable choice for any facility focused on improving cleaning performance and reducing operational costs.